水泥生产石灰石原料质量控制要求
凡是以CaCO3为主要成分的原料都叫石灰石原料,如石灰石、石灰石泥灰岩、白垩。在熟料煅烧过程中,CaCO3受热分解,生成CaO放出CO2。所以石灰石原料是水泥熟料中CaO的主要来源,它是水泥生产中使用最多的一种原料,在生料中约占80%,一般生产1吨熟料的需1.4-1.5吨石灰石原料。
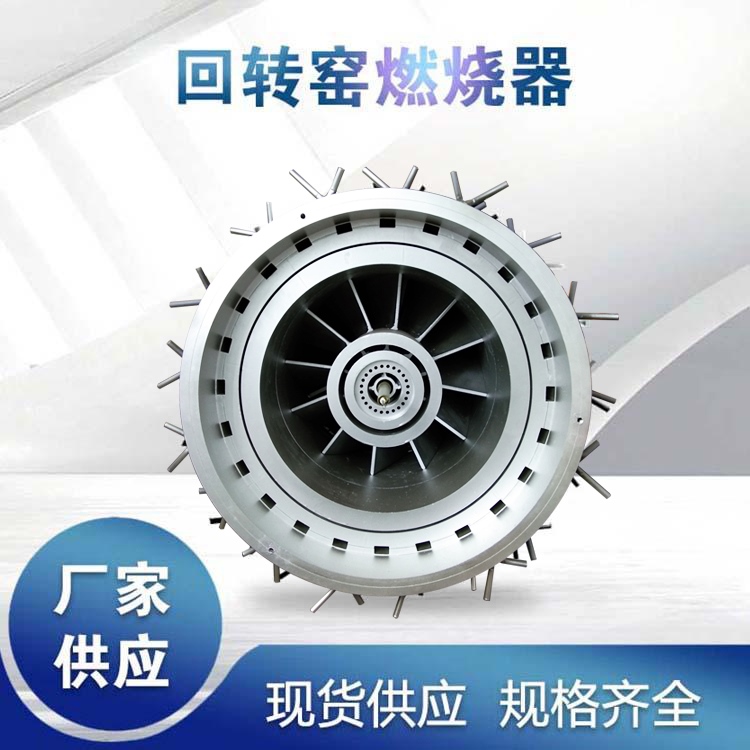
我国生产水泥的石灰石原料以石灰石最为广泛,泥灰岩次之,再次之为大理石,而白垩及贝壳仅一些小厂使用。石灰岩在我国资源丰富,分布也非常广,它是一种沉积岩,主要由方解石微粒组成,依成因可分为生物石灰岩、化学石灰岩和碎屑石灰岩三种。石灰岩中常有其他混合物,并含有白云石、粘土、石英或隧石及硫酸钙等杂质。石灰石呈致密状,纯净的石灰石是白色的,由于含有不同的杂质和杂质的多少而呈清灰、灰白、灰黑以及淡黄或浅红等不同颜色,常见的为青灰色,比重为2.6-2.8。
石灰石中的白云石(CaCO3、MgCO3)是熟料中MgO的主要来源。石灰石中的方解石矿物结构、结构形态、结晶体完整程度及晶体大小等都对熟料煅烧活性有着很大影响,同时其所含杂质多少、杂质成分、结构、分布状况,特别是隧石中的α-石英晶体,以及石英晶体的发育状况等,对生物的化学反应活性影响也很大,因此在对水泥窑系统分析研究中,也要考虑到这些因素。
石灰石的质量指标控制主要包括CaO、MgO、R2O、SO3、CI-等。其中CaO是构成生物的主要成份,是石灰石矿山前期勘探需查明的主要内容。较高的CaO、较低的MgO、R2O、SO3、CI-含量是优质石灰石矿山和生产优质熟料的基本要求,矿山选址的依据。
进厂石灰石的质量量指标控制属预配料控制过程,日常以控制CaO含量为主,即进厂石灰石品位。对于其中的有害成份,一般随石灰石品位变化:石灰石品位越高,有害成份越低;石灰石品位越低,有害成份越高。控制合理的进厂石灰石品位,是为了保证生料率值满足预计的要求。石灰石品位即非越高越好、也非越低越好,应根据所使用的硅铝质原料及生料率值要求来限定。
引起石灰石品位变化的因素主要是矿山断层、裂隙土、表层覆盖土、高镁夹石、薄层灰岩等。这些因素均会引起石灰石品位的贫化。矿山一经选定,其矿石中MgO含量应符合要求,实际生产中,应关注所用矿山的矿石中MgO含量的不规则变化,较高的MgO含量的不规则变化,较高的MgO一般是由高镁夹石所引起。在所用高镁夹石体的矿区时,应加强源头控制,注意搭配使用,确保进厂石灰石中MgO 含量满足要求。有害成份主要随石灰石品位变化,薄层灰岩、边坡料等是引起有害成份升高的主要因素。实际生产中,应根据矿区开采点的阶段性变化,均匀搭配薄层灰岩、边坡料等,注意保持石灰石品位的相对稳定,以保证有害成份在控制范围内。
石灰石品位的控制通过炮孔取样、炮堆取样、入均化堆场取样来跟踪完成。炮孔样是指导矿山台段开采品质跟踪的依据,炮堆取样是炮堆搭配的主要依据,入堆场取样是计算均化后的石灰石料堆整体品位满足配料要求的重要过程。通过以上过程的控制,可以保证入磨石灰石品位受控。